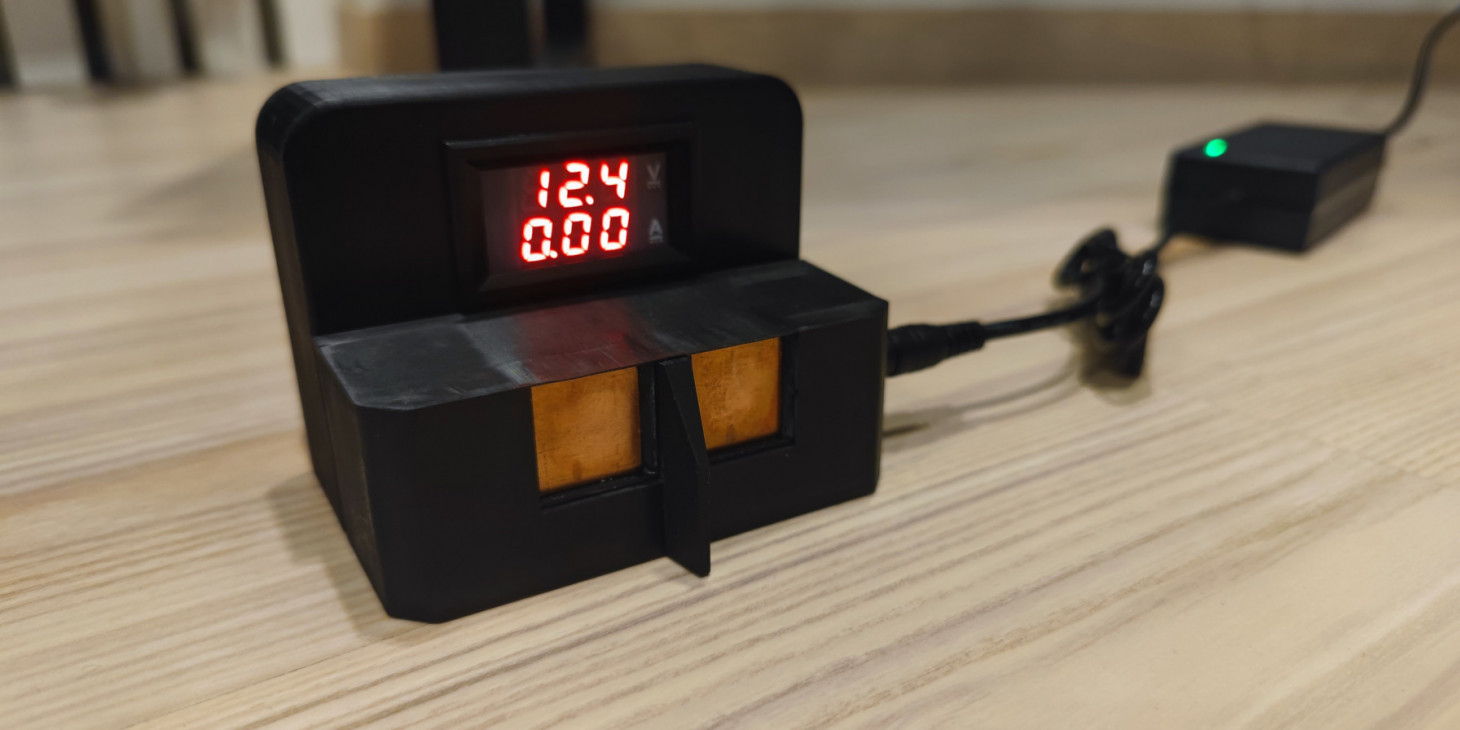
155
Проект смотритель. Часть 9. Зарядная станция
Эта статья является частью цикла
- Проект смотритель. Часть 1. Начало
- Проект смотритель. Часть 2. Дизайн
- Проект смотритель. Часть 3. Фоторезист
- Проект смотритель. Часть 4. Шасси
- Проект смотритель. Часть 5. Гусеницы
- Проект смотритель. Часть 6. Моделирование и печать
- Проект смотритель. Часть 7. Железо
- Проект смотритель. Часть 8. Софт
- Проект смотритель. Часть 9. Зарядная станция
- Проект смотритель. Часть 10. Bluetooth
- Проект смотритель. Часть 11. Home assistant
- Codex написал WASD управление для Смотрителя
Раз уж одна из целей - удалённое управление - стоит озаботиться вопросом питания.
Батарею расширять некуда - размеры и так минимально возможные. Значит, нужна зарядка, да такая, чтобы на неё можно было встать по видеосвязи. Также нужна индикация процесса заряда и некая контактная пара. Что-то подобное зарядным станциям роботов пылесосов, но из доступных средств.
Рассматривал варианты магнитных контактов, но ввиду кажущейся сложности реализации же остановился на подпружиненных. В теле робота я разместил штифты, а на зарядной станции пластины. В целях экономии места пружины и индикация будут на стороне станции.
Руководствуясь все той же избыточной надёжностью были приобретены медный пруток 5мм и пластины 20х20х1.5мм. Под них и был спроектирован корпус:
В качестве источника питания изначально планировал задействовать преобразователь 5v - 12.6v с usb type c на борту - характеристики обещали 3А тока:
Но дьявол крылся в деталях - 3А не на выходе, а на входе, помимо этого плата в отсутствие активного охлаждения быстро перегревается и выходит из строя, попутно оплавляя все вокруг. Из отзывов было установлено, что мощность можно снизить вдвое, выпаяв один из реисторов у входа:
Но и это не спасло, плата выдавала меньший ток и не так быстро грелась, но за минуту грелась градусов до 70-80, оставлять такое без присмотра не решился. В итоге все свелось к нормальному внешнему блоку питания, подходящее гнездо для разъёма которого по счастливой случайности у меня нашлось в закромах.
Детали получилось подогнать достаточно плотно, но без люфта. Пластины на 1 пружине в углу со стороны штифта работают идеально.
Что касается индикации - была идея собрать схему с 2 светодиодами, но, честно говоря, быстро не разобрался элементарной базой и принципиальной схемой, а время поджимало. Вместо них взял вольтамперметр и расположил на зарядной станции аккурат напротив камеры. По его показаниям будем определять статус заряда. Небольшой ток он, правда, не показывает и ориентироваться можно либо по падению напряжения, либо при большом разряде - уже на амперметр.
Финальный вид изделия таков:
Такой широкой станция спроектирована специально, чтобы сделать невозможным неправильный заезд на неё. Ширина на пару миллиметров меньше чем расстояние между траками:
Ну и робот, стоящий на зарядке. Фокусное расстояние камеры не позволяет видеть все чётко, но для индикации такого вида достаточно.
Картинка в трансляции выглядит так (от разрешения не сильно зависит из-за фокуса, но здесь оно низкое):
Что касается схемы зарядки - внутри стоит ещё 3S BMS плата, контролирующая заряд и обеспечивающая поддержание одинакового напряжения на банках. Можно было бы обойтись и без неё, многие заряжают 3s сборки напрямую, но я предпочитаю более безопасный вариант.
Из-за избыточной упругости пружин поставить робота на зарядку дело нетривиальное - он отпружинивает и остается без контакта, нужно ловить нужное положение. Думаю схема на магнитах, как у многих наручных часов, была бы легче в использовании. До её реализации я не добрался, возможно зарядную станцию будет ждать апгрейд.
Комментариев пока нет
-
Кросс-постинг инженерного DIY-контента
Начал выходить за рамки личного блога, кажется, что часть контента заслуживает… -
Композитная будка в стиле Сиднейской оперы. Часть 1
Как вам такой проект? Без электроники, но все еще с ИИ, 3д моделированием и еще… -
Грабли для выравнивания
Как-то так наложилось, что мне нужно обустроить новую площадку для газона, а со… -
Вкатываемся в видеоблогинг
Некоторые проекты на мой взгляд заслуживают более широкого охвата, видео в этом… -
Codex написал WASD управление для Смотрителя
В комментариях к ролику с демонстрацией Смотрителя меня давно просили добавиьт… -
Klipper на Two Trees Sapphire Plus
Случилось то, что давно назревало - штатная прошивка Marlin перестала меня устр…