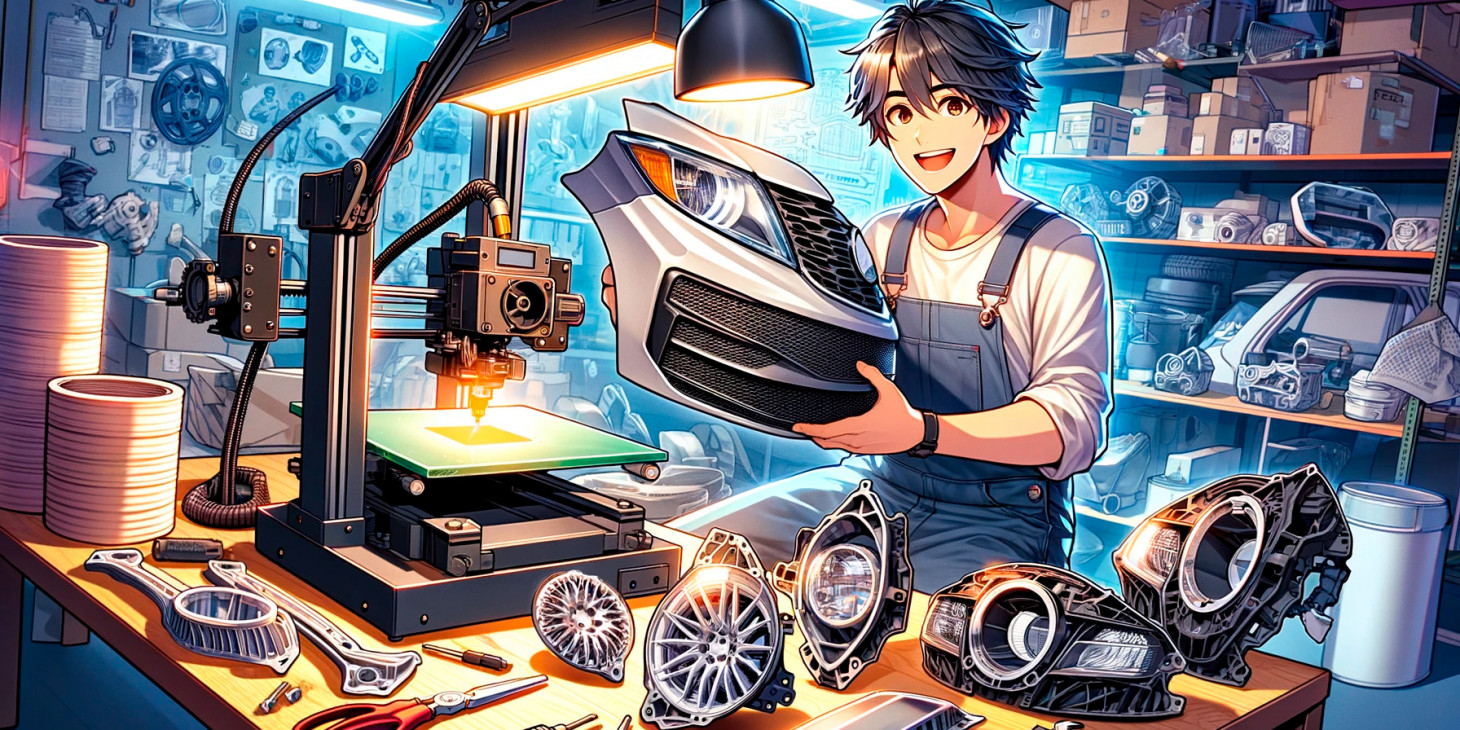
44
DIY Honda: Printing Parts in the Garage
Some years ago, an unfortunate incident occurred with my former car, a Honda Accord 8 — the headlight bracket along with the headlight mount snapped. It features a long bracket that breaks first upon any impact, which, however, protects the headlight from damage.
It happened quite simply, one summer night as I was returning home and decided to pull over onto a grass-covered shoulder. From there, unexpectedly, a water hydrant popped out at me. Luckily, the hydrant was loosely attached and deflected from the impact, but it was enough to damage the mounts.
So, what to do? In the summer, I glued the plastic back together and put it in place, intending to change the brackets later. And now the time has come, we're ordering:
71190-TL0-G01
right front bumper bracket ~$1006100-TL0-G01
right headlight repair kit $19
The repair kit is not at all what it seems by its name, and the cost for a small piece of plastic is also beyond...
Recently, I wrote in my personal blog about having a 3D printer, on which I printed a door limiter for a friend's Hyundai Elantra.
And since I already had the repair kit in my hands, especially at such a high price — I decided to reproduce the part myself. We take calipers, open CAD (SolidWorks), and spend several evenings drawing the model.
Everything seems okay, we load the model into the printing program (slicer), the shape of the part is quite complex, can't be printed without supports (auxiliary "stands" that are removed after printing):
Set the infill to 75%, 3 hours to print the part — that's not much
We compare the resulting parts with the original (no analogs are produced at all):
Found a couple of flaws — made a mistake in one place by 5mm, in another with the thickness of the part at the hole, so I made corrections to the model and reprinted.
If you ever wondered how the Chinese copy parts and produce analogs, it happens pretty much like this, except that instead of 3D printing, plastic casting is usually used, which is more massive, faster, and cheaper (on large batches). With printing done, we go to the car and drop the bumper (in winter, with wet snow — dubious pleasure).
This is how it rode for more than a year, causing no problems except for the fact that I was aware of it, also here you can see a couple of broken clips on the bumper bracket.
We remove the headlight, turn it over, and look at the broken bracket. From the factory, it is cast together with the headlight, and to install the repair kit, you need to saw off the factory mount and screw the repair kit into the factory places with screws (5x15mm screws).
The original leg is cut approximately along the red line.
I managed to cut it a bit shorter, it doesn't affect the work, but ideally, the old housing should rest against the repair kit for more rigidity:
Original and printed part — identical.
We install the original repair kit (so, did I just waste $19 on a piece of plastic?) and the new bumper bracket:
The bumper clips are in place, the headlight sits firmly.
And for comparison, who can guess where it was and where it has become?
And no one, nothing has changed externally.
So here's a link to all the necessary source files for the model — www.thingiverse.com/thing:4181855 The repair kit for the left headlight can be obtained by simply mirroring the model.
Printing parts is available in any city, easy to find. Prices in printing companies seem to be around $0.05-$0.10 / gram. My part ended up weighing 32 grams (the cost of the plastic itself in my case is $0.01 per gram — a kilogram spool costs $10.53).
No comments yet
-
Leveling Rake DIY Build
It all came together just right — I needed to prep a new lawn area, and suddenl… -
Getting into Video Blogging
Some projects, in my opinion, deserve a wider reach, and video content is unriv… -
Codex wrote WASD controls for the Caretaker
In comments to the video demonstrating the Caretaker, I was long asked to add… -
Klipper on Two Trees Saphire Plus
Something that was long overdue has happened - the stock Marlin firmware stoppe… -
Project Caretaker. Part 11. Home assistant
The project is positioned as remote monitoring, but how can you do that if the… -
Vibe-coding a Series of Articles in BoltCMS
We're creating support for post series using Cursor with Sonnet 3.7.