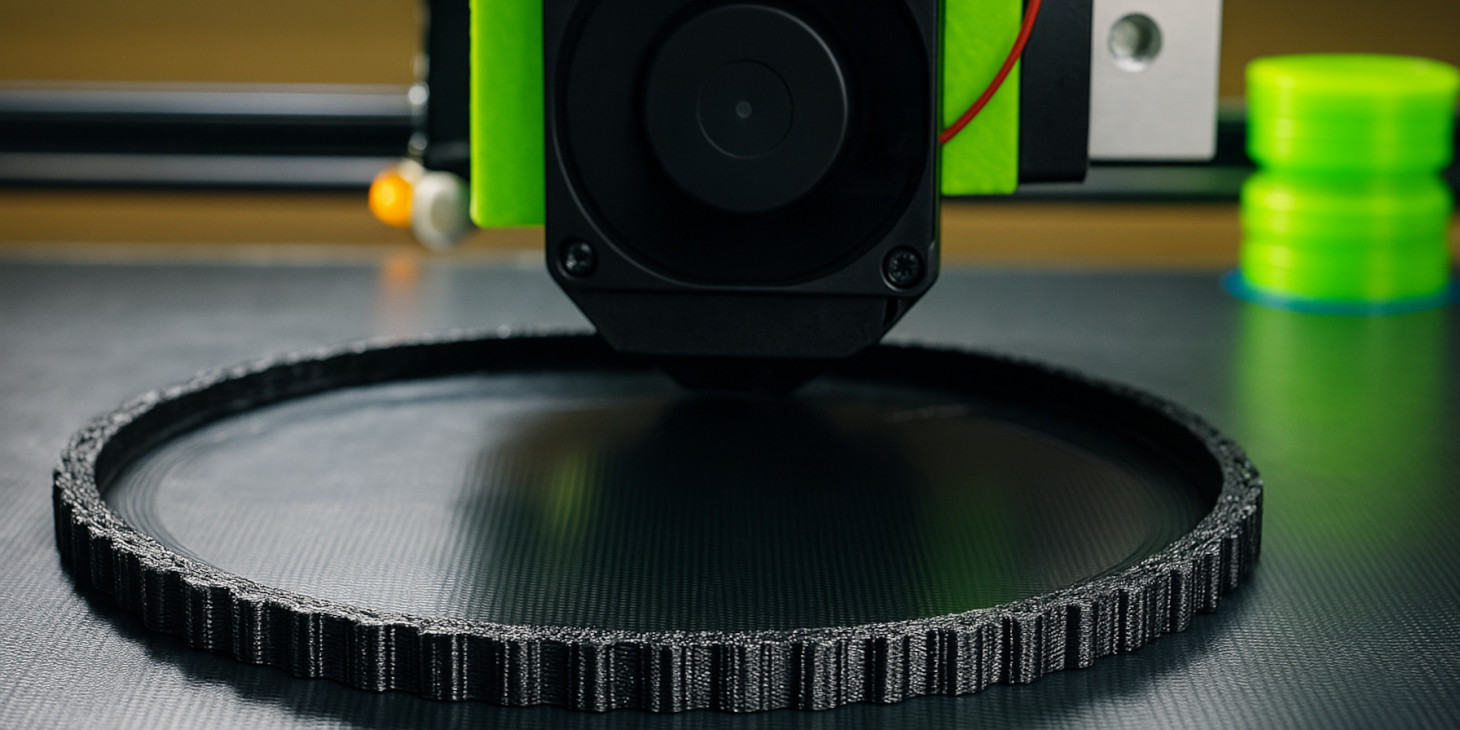
383
Проект смотритель. Часть 5. Гусеницы
Эта статья является частью цикла
- Проект смотритель. Часть 1. Начало
- Проект смотритель. Часть 2. Дизайн
- Проект смотритель. Часть 3. Фоторезист
- Проект смотритель. Часть 4. Шасси
- Проект смотритель. Часть 5. Гусеницы
- Проект смотритель. Часть 6. Моделирование и печать
- Проект смотритель. Часть 7. Железо
- Проект смотритель. Часть 8. Софт
- Проект смотритель. Часть 9. Зарядная станция
- Проект смотритель. Часть 10. Bluetooth
- Проект смотритель. Часть 11. Home assistant
- Codex написал WASD управление для Смотрителя
Шасси у нас уже есть, периметр известен, внутренний профиль определяется колёсами, внешний - дизайном.
На всякий случай напомню как выглядит дизайн и спроектированные колеса:
Вот так я спроектировал гусеницу:
Здесь есть несколько моментов, на которые нужно обратить внимание:
Печатать нужно круглую гусеницу, чтобы в ней не было никаких напряжений и неровностей структуры, которые могут впоследствии сказаться на плавности движения.
Параметры печати подобрать таким образом, чтобы структура была одинакова по всему периметру - по той же причине.
Вот так печатать неправильно:
Вот так нормально:
Так как мы печатаем круглую гусеницу, а колесо у нас меньшего диаметра - нужно предусмотреть возможность гусенице беспрепятственно сгибаться до нужного радиуса.
Нам нужно добавить некоторые "разрывы". В ходе изысканий по расчету нужного угла разрыва исписалась пара листов в блокнотике, но угол оказался настолько мал, что можно было запросто его увеличить в несколько раз:
Угол я взял избыточный - во время печати, тем более TPU, может произойти всякое. На фиксацию на роликах такой зазор не особо влияет.
Изначально взял основную толщину в 3мм - но напечатанное изделие оказалась перебором даже для меня, моторчики такую гусеницу крутили с трудом и рывками.
К тому же при такой толщине гусеницы слишком жёсткие - средние ролики оказались не задействованы.
Поэтому толщина была радикально уменьшена вместе с уменьшением высоты шипов - вышло 1.2мм (ровно 3 периметра при печати).
Пластик - bestfilament TPU soft. Пришлось печатать со скоростью в 20 мм/с, иначе даже директ экструдер не справлялся. По гибкости и прочности все более чем ок, пруток 1.75мм руками разорвать у меня не вышло, гусеница отлично подходит.
Единственное, где ожидания не были оправданы - зацеп. Поверхность по ощущениям где-то между пластиком и резиной, при перемещении без препятствий все ок, но может проскальзывать при упоре в препятствие - на стену уже не заехать.
Ну и печать не всегда идеально выходила, 1 раз зажевало пластик из-за ретрактов. Ещё раза 3 деталь превращалась в макароны либо появлялись пробелы в слоях. Одна такая гусеница за ночь допечаталась и её даже удалось спасти, заполнив пробелы 3д-ручкой.
Но эстетически она меня не устроила и была перепечатана.
Конечный результат c шасси можно посмотреть на видео ниже. Здесь еще наглядно видно как можно напороться, заказывая моторчики разными партиями или у разных поставщиков. И левый и правый были заявлены с передаточным числом 1:200, но по факту скорость отличается порядочно. А из разных партий моторчики оказались потому, что из изначально купленных 2 штук один решил заклинить и больше не заводиться. Поэтому дальше я заказал сразу 6 штук 1:150, чтобы никаких проблем не иметь (1:200 все же слегка шустроваты для этого проекта, хотя можно было бы и попробовать).
Комментариев пока нет
-
Image2model с tripo3d и Blender
Иногда хочется, чтобы нарисованный или сгенерированный персонаж стал настоящим -
Локальный эмулятор Telegram
Писали ли вы когда-нибудь телеграм ботов? -
Реанимируем основание вешалок
Есть дома пара вешалок с плечиками, на которых удобно располагается одежда для… -
Ложемент для столовых приборов
Органайзинг - одна из сфер, куда я периодически пытаюсь приложить руку. На этот… -
Кросс-постинг инженерного DIY-контента
Начал выходить за рамки личного блога, кажется, что часть контента заслуживает… -
Композитная будка в стиле Сиднейской оперы. Часть 1
Как вам такой проект? Без электроники, но все еще с ИИ, 3д моделированием и еще…